Carmakers are always looking for more ways to make their products more sci-fi, but how? Mostly this means electric cars and self-driving technology. This time it means 3D printing. Bugatti has developed the first 3D printed brake caliper and is looking to bring it to production.
The new caliper is unique in a number of ways, the first being its size. Its the largest caliper in the vehicle industry right now, besting the aluminum alloy brake calipers found on the Chiron. This printed piece is also not aluminum, but titanium instead.
The titanium part is an 8 piston monobloc brake caliper, allowing it to give a stronger performance over traditional metals. Bugatti states that it is capable of over 275 pounds per square millimeter of pressure. That's about the weight of an adult male pushing the edge of a paperclip. Despite the size and metal, the caliper is also surprisingly light. It weighs about 6.4 pounds, nearly 40% lighter than the aluminum contender.
This achievement was thanks to a partnership between Bugatti and Laser Zentrum Nord research institute. It took their printers 45 hours to create the part. This was done by using 4 powerful lasers to melt down the titanium, letting it drip down into place to form the caliper. This process heats the metal over 1,290 degrees. Once the part is drop formed into shape, it is brought into a milling machine to be refined. This takes 11 more hours.
Bugatti believes that production time will decrease as the process becomes more regular. 3D printing allows manufacturers to create a nearly infinite number of parts, reducing the cost of machinery significantly.
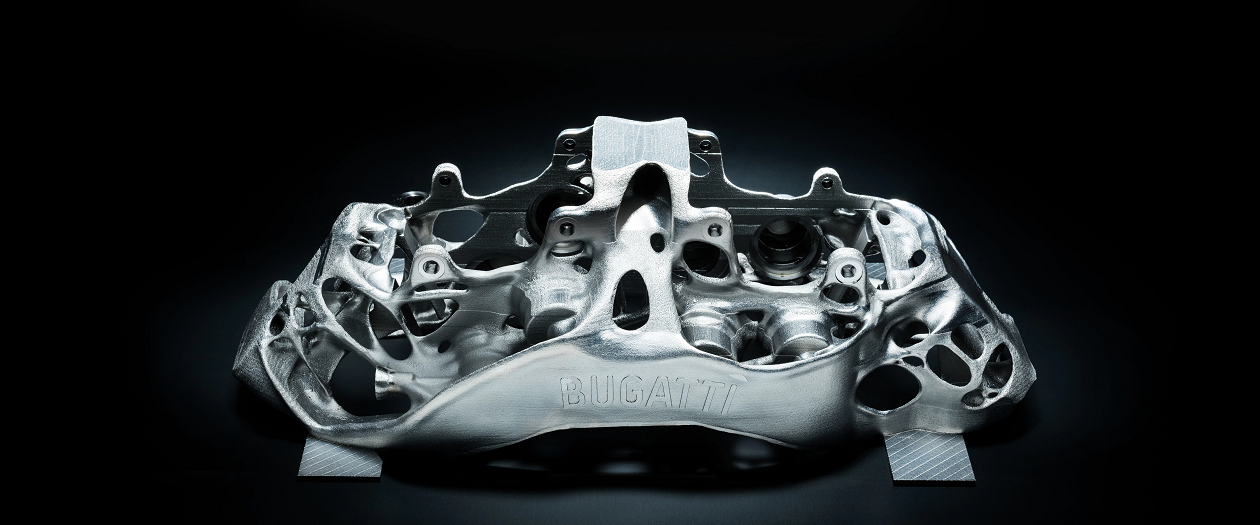
Bugatti Creates a 3D Printed Brake Caliper
Posted By: LizardRock | 0 Comment(s)
Posted On: Jan 23, 2018 @ 01:54 AM